In This Guide:
- Why Wood?
- 7 Styles of Wood Siding
- 7 Types of Wood Commonly Used for Siding
- Pros and Cons of Wood Siding
- How to Choose
- Cost Per Square Foot Installed
- Installation
- What Maintenance is Required?
Wood siding, or “cladding”, is natural, attractive material used to cover and protect the exterior of a house.
Some siding is designed for vertical installation, in a board-and-batten style. Others, such as shingles, clapboards, or shakes are installed horizontally. In North America, cedar and redwood are the most preferred types of wood used for siding.
The best wood siding options include 7 types of wood as well as 7 different styles and installation methods.
Why Wood?
Wood is natural, beautiful and durable which makes it a sought after siding option for use in traditional architecture such as cottages, bungalows and Cape Cod exteriors.
While the type and style chosen can cause the cost to vary significantly, it can be an economical siding choice to install on a house as it will last for as long as routine maintenance is done to maintain its durability and the rich look of the wood.
This guide presents an overview of the most popular styles used followed by the most commonly used types of wood in North America, approximate cost, and maintenance requirements. Each style can usually be ordered with either smooth cut or rough cut texturing.
7 Styles of Wood Siding
Some styles overlap, others are flush. Some are vertical, others horizontal.
Here are 7 styles:
1) Lap Siding
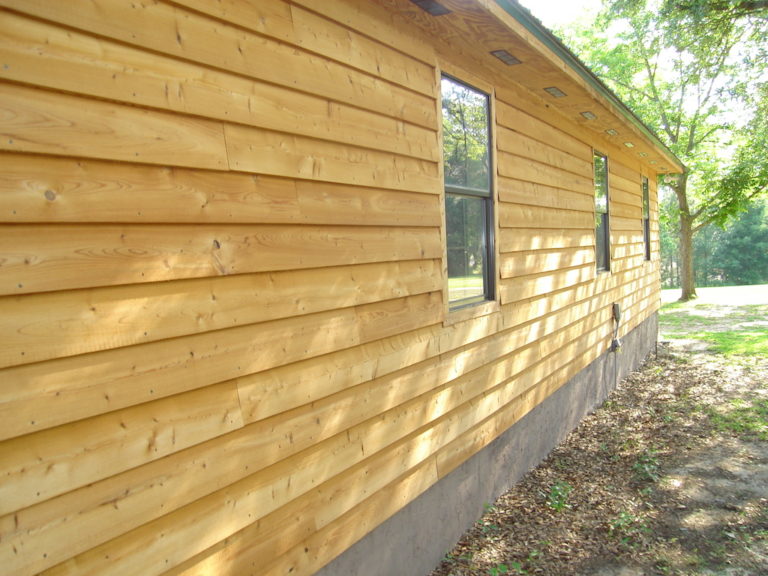
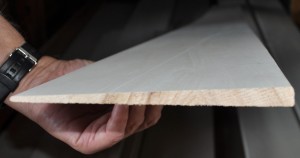
Also known as bevel or clapboard siding, lap siding is a traditional style of cladding going back to the early days of the U.S. It is still in use today because of its appearance and durability.
Lap siding is created by sawing a board lengthwise in a slight pie-shape. This creates a narrow edge on one side of the length of the board, and a wide edge on the other side. The contractor will overlap the boards, starting with the first board placed at the bottom of the wall. This overlapping is where the term “lap siding” originates. This type of siding sheds water quite well, as there are no edges that will hold and absorb moisture.
Each contractor makes the decision regarding how much to overlap the boards. The exception to this is lab siding that has grooves inset. This predetermines the amount of exposure left. The more overlap there is the sturdier the structure will be. The average exposure is four to eight inches. Smaller exposure area has a more expensive look.
Lap siding must be maintained with periodic staining or painting. Caulking will be necessary to reduce weather damage.
2) Drop Channel Siding
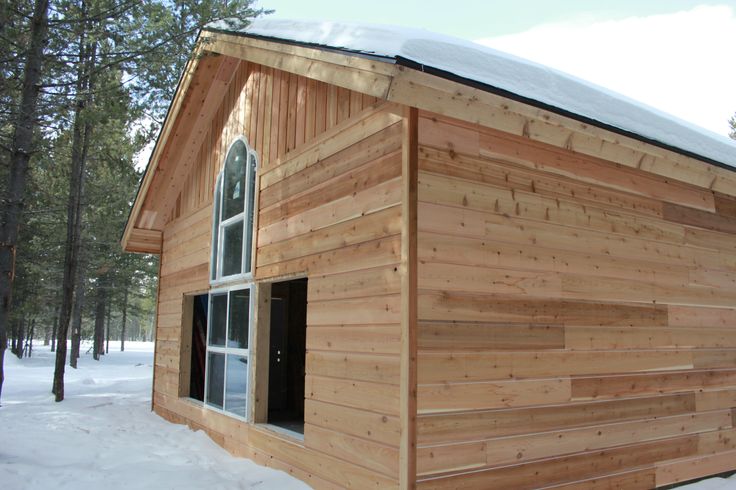
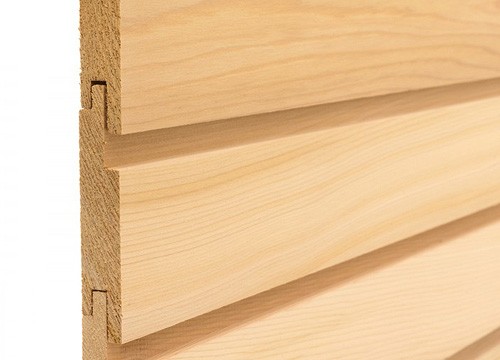
Drop channel siding is versatile in that it can installed horizontally, diagonally, or vertically. This type of siding is a popular choice for cabins as many cabins are paneled with boards cut with the drop channel style.
One long edge of a plank is milled down to be significantly narrower than the rest of the board. On the other long edge, a small groove is cut on the bottom of the board. This creates an overlap that shows the sculpturing of the board without creating a ledge on which water can bead.
One of the benefits of drop channel siding is that it gives wood plenty of room to expand and contract without compromising the structure. The partial overlapping and beveled edge create an interesting shadow line.
Rough-hewn knotty pine is often milled into drop channel siding, and valued for its rustic appearance. Drop channel siding can be special ordered in prefinished grades of whichever wood is desired. It requires the same maintenance of any other wood siding, with periodic power washing, and painting or sealing.
3) Tongue-and-Groove Siding
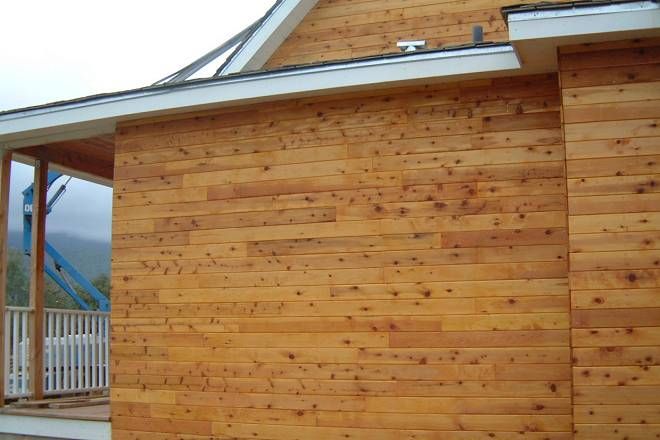
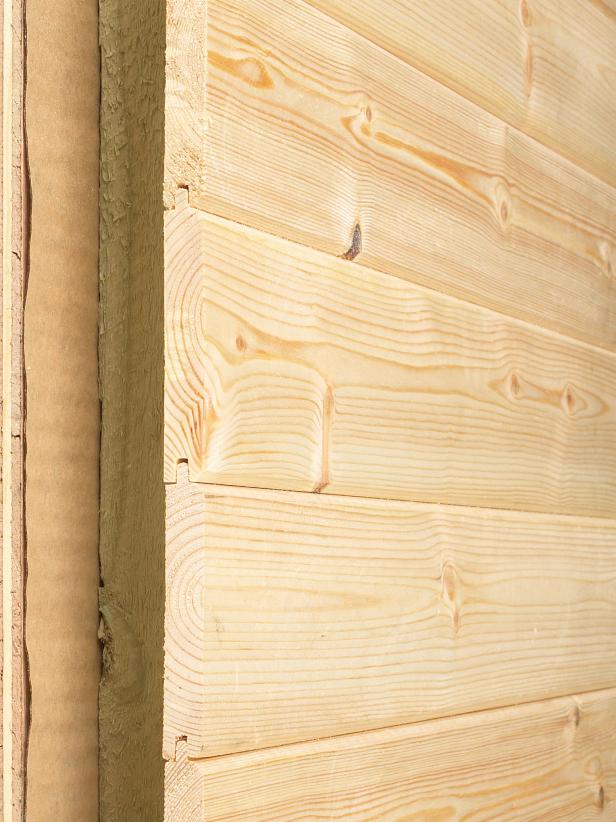
As with the drop channel siding, tongue-and-groove siding can be installed in any desired direction: vertically, horizontally, or diagonally. It is available in rough cut or smooth cut, and is made with either clear wood or knotty pines.
Individual planks are milled with a groove on one long edge, and a corresponding tongue on the other long edge. The tongue-and-groove planks interlock to create a smooth surface. This is the type of joinery used for hardwood floors, but it is also used for siding.
This is one of the most sturdy of construction methods, as there is uninterrupted contact between the boards, running the length of the planks. Most antique hardwood floors are made of narrow strips of tongue-and-groove oak, maple, or walnut planks.
4) Split Logs
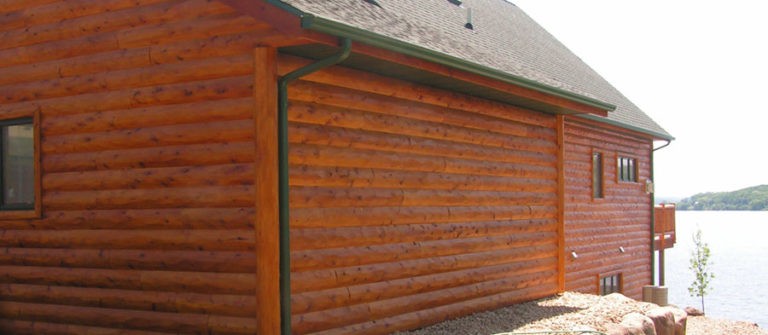
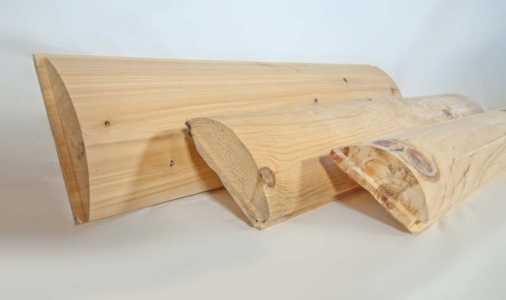
The traditional log cabin look is particularly popular in woodland settings, and can establish a cozy ambiance regardless of the size of the home. Split log siding is custom made, and is usually made from a hardwood, such as cypress, cedar, or oak.
The wood must be sawed with the natural bark still attached. This section is then attached to the prepared wall. They appear to be solid logs. These planks must be dried before installation so that shrinkage does not cause failure of the siding.
Most applications are sprayed with a clear-coat to seal out moisture and insects. Maintenance is similar to that of other wood siding, with maintenance of the clear-coat. In addition, any cracks that appear in the split log siding must be filled and sealed to prevent sloughing of the bark.
5) Board-and-Batten
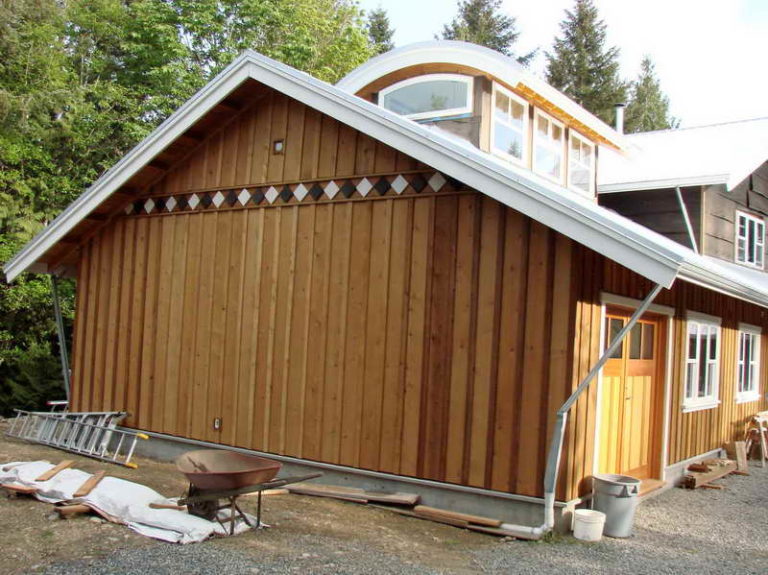
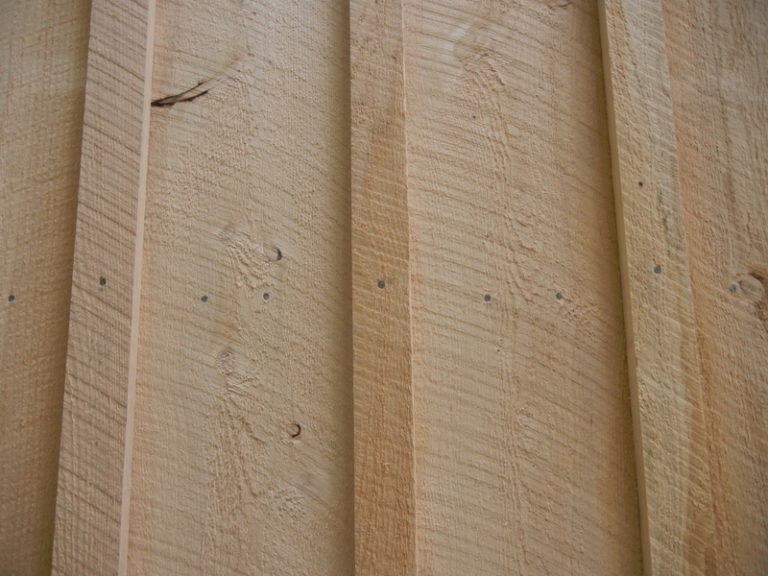
Another historic style of covering the outside or inside of a house is with board-and-batten siding. This has been most frequently used in completing barns and other farm buildings. The siding is installed vertically, and consists of wide boards that are spaced evenly, with a batten nailed over the space. The batten is a narrow strip of wood.
This manner of installation allows for more expansion and contraction of the planks. It is thought that this method of construction was developed in order to allow farmers to hang siding with unseasoned wood.
One popular application of board-and-batten siding is to use varying widths of boards and battens to create different patterns.
6) Shake Siding
Shakes look like shingles, but they are much thicker and more durable. The bolts, or wooden blocks, from which they are cut, are sometimes hand-sawn. The shakes are not uniform in thickness, which is part of the appeal of shake siding.
The individual shakes can be purchased in 16, 18, or 24-inch lengths. They are attached to the sheathing, starting at the bottom of the wall. Each layer overlaps the previous one. Shake siding is mostly available in redwood and cedar. It has a rustic, coarse look.
It is important to check building codes in your area before you install shake siding or cedar shake shingles. Some building codes prohibit these products, citing the fire hazard of that much rough-finished wood. Shake siding should be treated with fire-retardant chemicals and maintained to keep them from splitting or hosting insects.
7) Shingle Siding
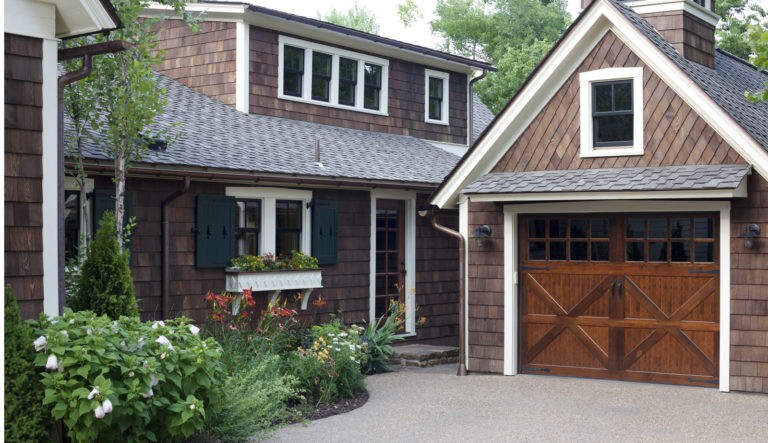
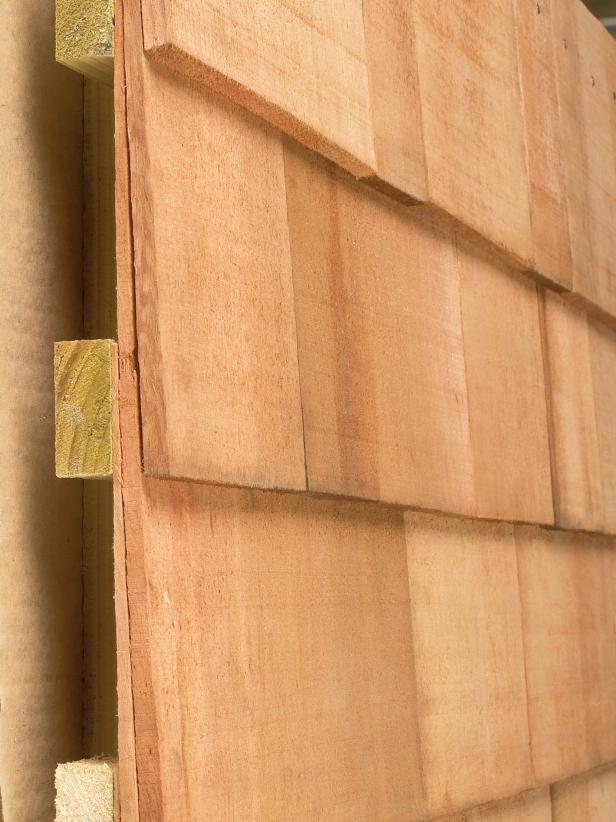
Wood shingles are popular for siding applications because of the smoothness and consistency. They are fairly easy to install, and preferred for oddly shaped walls such as turrets. They can be stained or painted, and are often painted in bright or historic colors when used on Victorian style homes.
Shingle siding can be made from any of the woods used for other types of siding. However, they will need to be treated to make them fire-retardant. As with the shake siding, check with local building codes. Areas that see frequent fires may not allow shingle siding. Maintenance is necessary to keep the shingles from drying out and becoming damaged or insect-infested.
What Style Do You Prefer?
7 Types of Wood Commonly Used for Siding
There are 6 kinds of natural wood that popularly used in the U.S. and Canada as well as engineered wood (a man-made alternative). They are a mixture of hardwoods and softwoods, with some variation in the density of the wood.
1) Cypress
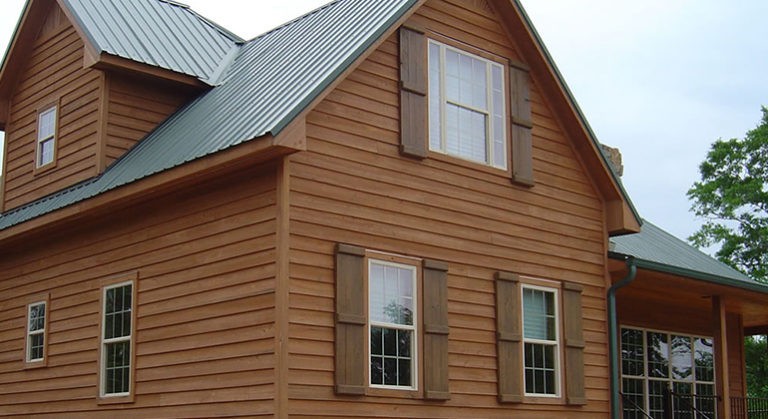
Cypress is a hardwood and highly desired as a siding application. It is extremely durable, often being salvaged from demolished centuries-old homes for reuse.
Cypress, like cedar and redwood, is rot-resistant and insect repellant. This made it the preferred wood in early America for use as water reservoirs. It is quite lightweight in comparison to its density and woodgrain.
Being a hardwood, cypress is difficult to mill. This, along with its expense, makes it uncommon in modern applications.
2) Redwood
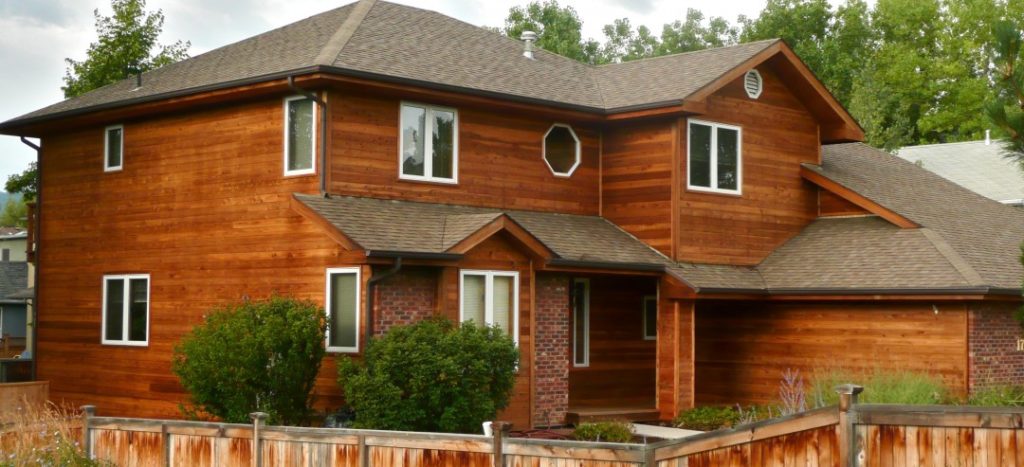
Redwood is one of the most durable and preferred woods used in siding. The wood has very little resin, so it accepts stain or other finishes easily. The wood does not shrink as much as other types of wood, so it doesn’t change shape as much. This reduces cupping and warping. For these reasons, redwood siding requires less maintenance than other types. Simply power wash it once a year, and seal it every three years or as needed.
Redwood siding also has natural insect repellants and is not as prone to rot. This discourages insects such as carpenter ants from destroying the wood and reduces the chance of insects burrowing between the siding and moisture barrier to nest.
Redwood is grown in the western part of North America. For that reason, it may be difficult to obtain in other parts of the continent. Redwood siding costs between $8 and $20 per foot, uninstalled.
3) Cedar
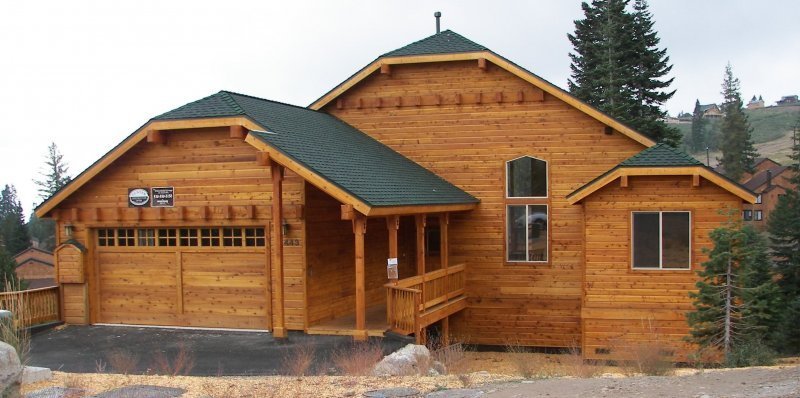
Cedar siding is sturdy and relatively easy to work with. This, too, is slightly harder than other softwoods. The straight grain makes this a very stable wood when turned into siding, and provides a beautiful finish when stained, making this the preferred wood when a stained finish is required.
As with redwood, cedar siding is less likely to cup, split, or swell. It is structurally sound and is resistant to insects and rot. One of the two harder of the softwoods, it typically has red and white woodgrain, with the red being called the “heartwood.”
The amount of heartwood usually determines the price, as it is this feature that makes the wood stronger and more insect resistant. While heavily variegated cedar is still a good choice for wood siding, the boards with more heartwood are preferable. This is most commonly called red cedar.
Clear, Grade A cedar is more expensive, and is available in different grades.
Maintenance of cedar siding is relatively simple, as with redwood. It requires annual power-washing and renewal of stain or paint every 3 years, or as needed.
4) Fir
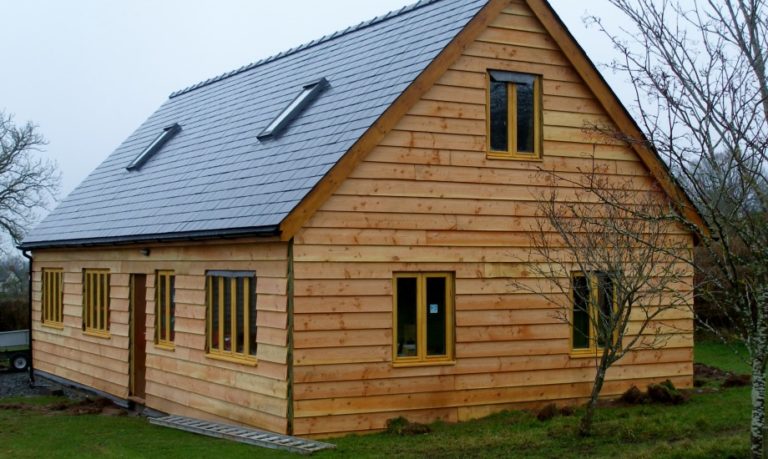
A very popular option is fir. This is a true western softwood, and is available as longer boards. This wood is easy to cut, with little sap or resin to clog saw blades. This makes it a popular choice for types of siding that require more milling, such as tongue-and-groove.
Fir siding has an even grain that receives finishing well. It is more common to paint fir, although the grain looks fine when stained.
Fir is not naturally insect resistant, nor is it rot resistant. Therefore, it requires regular maintenance to make sure it is not absorbing moisture or hosting destructive insects. It must be sealed with paint or stain to maintain its integrity.
The quality of lumber determines the amount of warping, cupping, and shrinkage. Unlike redwood and cedar, this softwood will absorb moisture and warp.
5) Spruce
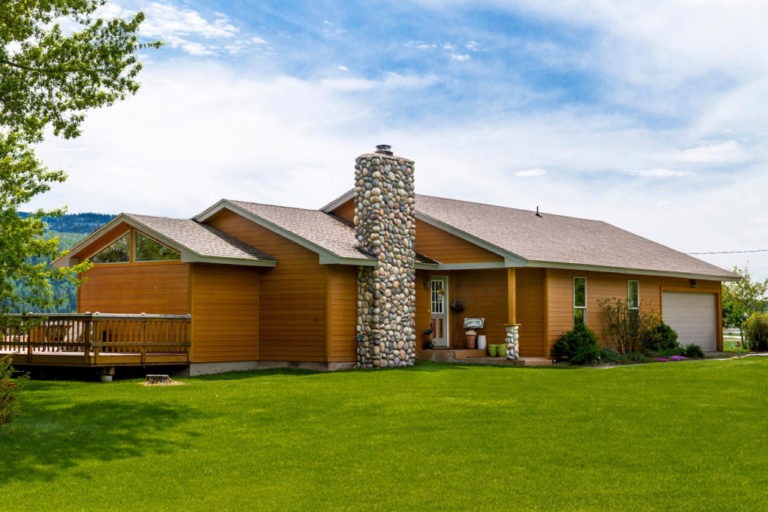
The spruce tree is a member of the pine tree family. It is most commonly found on the East Coast. Since it has many of the same characteristics of pine, it is often used to manufacture wood siding.
Spruce siding is often available in longer lengths than normally found with pine. Since it is a softwood, it can be milled into different styles of siding.
Spruce is not rot resistant, nor does it repel insects. Like fir, spruce siding must be maintained to keep it from absorbing moisture and rotting or warping. It is available in different grades, which affects the price.
6) Pine
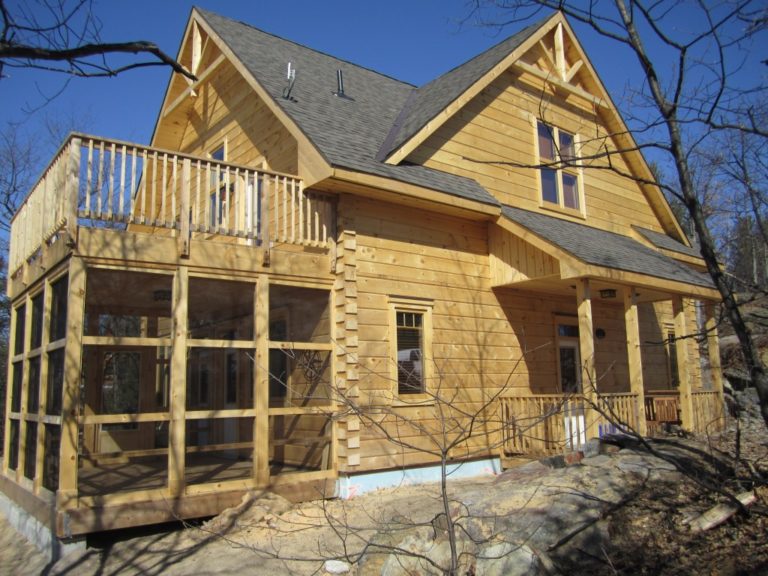
By far the most common wood found in siding in North America is pine. White pine is used in finish projects while yellow pine is used for framing. This is because yellow pine has a hard, yellow streak alternating with white. The yellow section is full of sap that rejects paint and stain and gums up on saw blades in milling machines.
White pine can be painted or stained, with paint being the most common application. This is because pine does not have a distinctive grain. It may be hard to find long boards of knot-free pine. In addition, the wood from fast-growing species of pine tends to split and check. Contractors look for higher quality pine siding that will be more durable.
Pine is not rot resistant, and does not repel insects. It requires paint or stain to seal it and retain the integrity of the wood. However, the softness of the wood makes it easier to mill to produce different styles of siding.
7) Engineered Wood Siding
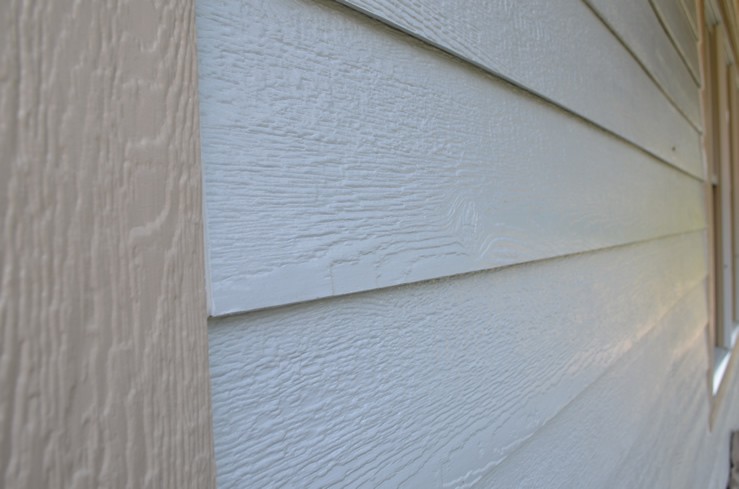
Engineered wood siding is extremely durable, lasting upwards of 30 years when properly maintained. It is manufactured using woodchips and sawdust, along with other castoff wood, combined with bonding agents.
The result is a strong, lightweight product that is easily milled and available in variable lengths. It is generally easier to install, since there are no flaws or knots to work around. It is also easily milled into any of the styles of siding preferred.
There are finishes applied at the factory, but engineered wood siding will need to be painted and maintained.
What Type Do You Prefer?
Pros and Cons of Wood Siding
Pros:
Impact resistant
While brick will chip under impact, and metal will dent, wood will gradually “ease” out dents. The fibers of the wood continue to respond to moisture content and temperature, making it more impact-resistant.
Beautiful
The natural beauty of wood is highly valued by designers and homeowners.
Easy to install
It can be installed by non-professionals, if they are reasonably skilled.
Easily manipulated
It can be cut and shaped to fit difficult areas or oddly shaped walls.
Cons:
Maintenance
It requires more maintenance than vinyl, metal, stucco or brick siding. This adds to the total cost of the siding over time.
Expensive
It is more expensive than vinyl, and high-grade cuts can be very costly.
Damage
Wood used in finish surfaces may warp or cup. This makes it important to purchase quality materials and install them properly.
Vulnerability
Many species of wood is vulnerable to insects, and most of them are vulnerable to water damage if not properly sealed and treated.
Eco-Friendly
It is actually considered to be an eco-friendly solution in construction because the product degrades quickly in landfills. It can also be reused, with planks and beams from antique buildings reused for hundreds of years.
How to Choose Wood Siding
The first step in selecting siding is to consult with your building contractor. Local professionals will know what types of wood are best for your uses. They will also already have vendors from whom they can order their supplies and rely on timely delivery.
Local contractors can also advise you on the availability of different types. If the job requires a wood that is not harvested very often, or that is shipped a long way, it can cause expensive delays to the construction. It will also be expensive. In some cases, a particular kind will not be a good choice because of the temperatures and moisture levels of your region.
Purchase the highest grade of wood siding possible. Look for wood that is:
- Insect resistant
- Rot resistant
- Clear of splits and checks
- Straight and flat
Most local contractors will allow a shipment of wood to acclimate to your region before installation. This crucial step reduces the likelihood of cupping and warping. Then, when the wood siding is installed, keep it properly sealed and protected.
Cost of Wood Siding Per Square Foot Installed
When you purchase wood siding, expect to spend $5 to $10 per square foot more for siding and installation. Shingles and shakes typically run from $6 to $9 a square foot, where wood clapboard can cost as little as $5 a foot. The installation does not include staining, but should include caulking around window and door frames and sealing edges.
For a two-story home, you can expect to spend between $14,000 and $23,000 for wood cladding installation. Adding accents of shakes or shingles will push the final cost to the high end of that range.
Installation
Basic installation of natural wood siding requires a solid, flat surface covered with a moisture barrier. Plywood is typically used for the flat surface, with the moisture barrier placed between the plywood and siding.
The method with which the siding is attached to the plywood is determined by the installer or the unique needs of the siding itself. It may be applied with construction adhesive or require screws or nails. The siding is then sealed with either stain or paint, and caulk is used around edges such as window and door frames and to fill in any gaps between panels.
What Maintenance is Required?
Wood siding requires regular maintenance to protect your investment. Factory finishes tend to last longer, but they can be more expensive. You may also have limited color choices.
Factory primed pieces are a good compromise as they will just need to be painted afterward.
If the wood has an attractive grain or striking texture, it is sometimes stained. Stain should be reapplied every three years, while clear finishes will need to be updated every 2 years. Paint will usually last much longer – up to 5 years.
Moisture will create rot and/or mold, so it is important to make the siding as waterproof as possible. There should be a moisture barrier directly beneath the siding, and special attention should be given to joints and knotholes.
Sealing the siding with stain, paint, or a clear finish will cost between $2,000 and $5,000. With proper maintenance, though, you will have beautiful siding for many years.
What to Read Next
8 Best Siding Options – Pros & Cons
Over to You
We’re interested to know – have you had wood siding installed in the past? If you’re thinking of installing it, what type and style are you leaning towards and why? Let us know by leaving a comment below!
I see you did not list shiplap, which has a unique look and has been experiencing a bit of a resurgence ?